Veltins - Smart valve monitoring for the secondary circuit
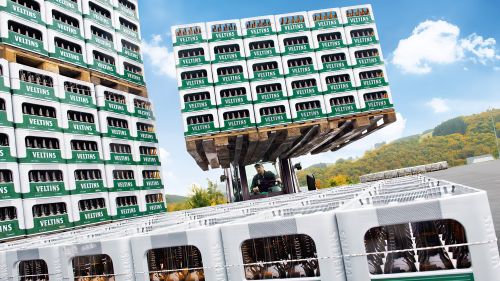
The C. & A. Veltins brewery relies on MVQ valve sensors supplied by ifm
Transitioning tradition into the modern age that is one way to describe the history and development of the German C. & A. Veltins brewery, headquartered in Grevenstein, over nearly two-hundred years. What started as a country brewery has become one of Europes largest and most modern private breweries, producing over 3.36 million hectolitres annually at the last count.
Whether it concerns electricity, innovative brewing and bottling technology or its own waste disposal plant: Time and again, C. & A. Veltins has trodden new paths, set sector standards and devoted itself to sustainable use of natural resources especially the spring water that emerges right next to the brewery.
Exactly controlling the temperature
C. & A. Veltins CEO, Peter Peschmann, explains that this spring water is not only used for brewing, but also as a means of heating and cooling. Whenever our products need to be heated or cooled during the process, we do that by means of water. Brought to the right temperature, the water is available via the secondary circuit. Inflow and outflow are controlled by valves. To ensure uniformly high product quality and keep wastage to a minimum, we need to control the flow of water exactly and reliably all the time. This, in turn, means that it is very important that the valves function without a hitch.
Easy to use, solid quality, precise data
Previously, the valve flaps were monitored with the aid of two proximity switches per valve that determined the flap position. These sent a switching signal to the controller, either valve open or valve closed.
Technology CEO Peter Peschmann explains: Quite apart from the need for dual cabling, this method was especially prone to failure in the hot water pipes, because the inductive sensors supplied previously by another company could not cope with the temperatures over long periods of time.
The MVQ valve sensor is a reliable and also easy-to-use alternative, and it is successively being implemented by ifms automation specialists. It is mounted on the axis of rotation of the swivel valve. From there, it registers the position of the valve flap continuously and with an accuracy to the nearest degree and transmits the data via analogue signal to the controller. It can also transmit the data via the digital IO-Link communication protocol, with even more detailed diagnostic information. For instance, slower-than-expected flap movements or failure to reach the exact end position on account of wear or deposits are registered by the sensor, and the results are sent to the PLC for further processing as well as being displayed locally via LED. Switching points can be set freely so as to allow for simple integration into the control program.
Fewer losses genuine benefits
Thanks to the exact registration of the angle and the movement times via IO-Link, we are able to detect deposits at an early stage and plan the flap maintenance in the best possible way, explains Peter Peschmann. A case has already arisen in which the capacity to detect even very small flap openings was a great help to the company.
We were losing water in the circuit, and we couldnt localize the cause because there are no inspection visors installed in our large pipes. The MVQ then enabled us to find out that one of the valves was not closing completely. The valve was then rendered serviceable again at short notice, putting an end to the water losses. This demonstrates the potential and options that precise valve monitoring open up. For C. & A. Veltins, the MVQ represents real progress on our way towards reducing water losses as much as possible.



Image 1: The hot water needed during the production process is kept in a separate pipe system. Inflow and outflow are controlled via valves. The green LED on the MVQs shows: The valves are open.
Image 2: The position of each individual valve is visible from afar thanks to the MVQs informative LEDs. In the Veltins brewery, permanent red means: valve closed. Altogether, the MVQ provides seven colours for coding status.
Image 3: Veltins already has around 40 MVQs in its heating and cooling systems. Data is transmitted either via digital IO-Link communication, or analogue.
The status: clear as daylight
The MVQs display showing the current valve status by means of easily visible, multi-colour status LEDs was another decisive factor influencing Veltins decision to install the sensor successively on all swivel valves in the cooling and heating circuits of the brewing and bottling processes.
The main plus-points in favour of the sensor are the clear status display, the closed housing, the ease of installation that only requires a standard unshielded M12 cable, as well as the capability to gather all the data supplied by the sensors at the central IT level, says Veltins technology CEO Peter Peschmann.
Over ten years of cooperation in mutual confidence
To date, around 40 ifm valve sensors are now in operation in the C. & A. Veltins brewery, of which some operate in analogue mode, and some have an IO-Link connection.
We are convinced that the IO-Link brings added value regarding plant availability, says Peter Peschmann. Initial projects involving vibration monitoring were also successfully implemented prior to the use of the MVQ. Altogether, we have already been working with ifm for over ten years. Starting with the quality and usability of the products all the way to the competent, collegial support and advice with regard to further development of our automation solutions, we are very convinced of the value of this cooperation.

Hops, malt, water: the ingredients for a classic Pilsner beer. To ensure that the result really tastes good, the temperature has to be exactly controlled during the brewing process.

Conclusion
With high-quality products and expert support from ifm, the C. & A. Veltins brewery can ensure reliable functioning of the heating and cooling circuits, and set up the automation solutions in a forward-looking and resource-saving way.